Air Valves
Theory and Use of Air Valves
Air Release Valves and Air/Vacuum Valves are essential components to total pipeline design. Without these essential valves, pipeline capacity will be reduced 5-10% or more due to air pocket build up in the pipeline.
This reduced capacity may go unnoticed because air is an invisible culprit in pipelines. Not only will pockets of air rob precious line capacity, but entrapped air will also rob precious electrical energy. The pump will have to operate at a higher head to overcome the constricted flow. The elimination of air pockets minimizes the problem and greatly improves the pipeline efficiency.
Air Release Valves and Air/Vacuum Valves have a fairly simple construction and are relatively inexpensive. APCO’s years of experience have proven almost without exception that the cost of air valves is less than one percent of the total installed pipeline cost.
Air Release Valves represent low cost insurance for protection of expensive pipelines. Furthermore, the Air Release Valves pay for themselves by eliminating air pockets and maximizing the capacity and operating efficiency of the pipeline. Additionally, protection against pipeline damage will also occur because air pockets are a major factor in surge pressures and water hammer in a pipeline.
What are the main types of Air Valves?
There are two main types of air valves:
- Air Release Valves (typically with small orifice sizes of 1/2” diameter or smaller)
- Air/Vacuum Valves (typically with large orifice sizes of 1/2” diameter or larger)
When Air Release Valves and Air/Vacuum Valves are combined, they become
- Combination Air Valves (sometimes called Double Orifice Air Valves)
Where should air valves be installed on pipelines?
Air/Vacuum Valves or Combination Air Valves should be installed on all pipeline high points and changes in grade. Air Release Valves or Combination Air Valves should be installed on those high points where it is possible for air pockets to accumulate. Also, Air Release Valves should be installed at intervals of 1,500 to 2,500 feet on long horizontal runs lacking clearly defined high points. Installing manways at intervals in larger size pipelines provides an excellent point to install Air Release Valves.
What size air valves are required?
Air Valves can be sized by using the graphs and formulas in the APCO Air Valve Selection & Sizing Guide or
by using the APCO Air Valve Slide Rule. Contact your local DeZURIK representative for assistance.
To size air valves for a complete pipeline, your local DeZURIK representative can create a complete pipeline profile with recommended valve styles and orifice sizes using our APSLIDE software program. Contact your local DeZURIK representative for details.
Air Release Valves:
An Air Release Valve is used to eliminate small air pockets that form at the high points of a pipeline and restrict flow. Air pockets reduce pipeline capacity and increase the amount of energy required to pump fluids. DeZURIK manufactures three main styles of APCO Air Release Valves:
Air Vacuum Valves:
Air/Vacuum Valve are used to protect pipelines from damage by expelling or admitting large quantities of air. Air/Vacuum Valves expel air when filling the pipeline and admit air to relieve a vacuum when draining the pipeline. DeZURIK manufactures two main styles of APCO Air Vacuum Valves:
Combination Air Valves:
Combination Air Valves combine the functions of both an Air/Vacuum Valve with an Air Release Valve. Combination Air Valves, in either single to dual body types, are typically installed on all high points of a system where it has been determined that the functions of both an Air/Vacuum Valve and an Air Release Valve are needed to vent and protect a pipeline. DeZURIK manufactures four main styles of APCO Combination Air Valves:
- ASU Single Body Combination Air Valves
- AVC Single Body Combination Air Valves
- AVV Dual Body Combination Air Valves
- ASC Single Body Sewage Combination Air Valves
Vacuum Relief/Air Inlet Valves:
Vacuum Relief/Air Inlet Valves are normally closed. If the system pressure becomes negative, the Vacuum Relief/Air Inlet Valve will immediately admit air into the system and prevent a vacuum from forming. When system pressure returns to positive, the Vacuum Relief/Air Inlet Valve closes air tight.
Surge Check Valves:
A Surge Check Valve is used to prevent critical shock conditions from occurring in installations where the operating conditions cause a regular air valve to slam open and/or closed. The Surge Check Valve reduces the rate of flow of water into the air valve by means of throttling orifices in the disc, thereby preventing water hammer. This Surge Check Valve provides this slow closing feature and is mounted on the inlet of the Air/Vacuum Valve.
Double Acting Throttling Device:
Air/Vacuum Valves can efficiently discharge air from deep well pump columns when combined with a Double Acting Throttling Device. The Double Acting Throttling Device is fitted on the discharge orifice of the Air/Vacuum Valve. Because the pipeline media does not contact the Double Acting Throttling Device, it can be used on pipelines containing dirty fluids.
Contact DeZURIK Today to Get Started
Click the images below to find additional information about any of these high quality APCO Air Valves. Use the Find A Rep, Get A Quote or Contact Us links to request more information. We look forward to helping you select a valve for your application!
WHY DO YOU NEED AN AIR RELEASE VALVE IN A PIPELINE?
Air in a pressurized closed-pipeline system can have many effects. When air is present in a hydraulic pipeline, flows are erratic, unpredictable and have high head losses. Air may enter a piping system in many ways:
- Air in the pipeline when initially filled may not be completely purged.
- Air may be drawn in at a pump inlet by entrainment if the liquid level falls below the inlet elevation.
- Air in solution (about 2% by volume) will be released at points in the pipeline where the pressure is reduced, especially where the line elevation is close to the hydraulic gradient.
- Gas created from digested sewage.
- Air may be drawn in through the packing, seals and flanged joints.
- Air may enter by vortexing at the pump.
An air pocket will decrease the cross-sectional area and increase frictional pressure loss. The combined loss for two-phase flow (air and water) is always greater than the pressure loss for each phase flowing alone. Thus, air in a pipeline increases system flow resistance and increases system head against which pumps must operate.
Air in piping tends to collect at high points in the line when flow velocities are low. If the air pocket formed is large, part of it will be removed when the velocity increases. This partitioned air may or may not go through the system, depending on velocity, pipe size, and pipe down-slope. Air may only move into the sloping straight section and then return to the summit when the velocity decreases.
While it is impossible to totally prevent accumulation of air (or gases) within the piping system, the volume can be greatly minimized by installing APCO Air Release Valves on pipeline high points.
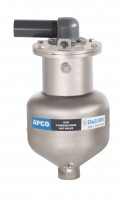
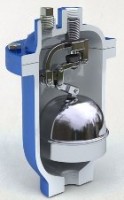
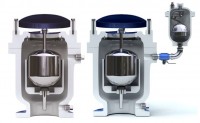

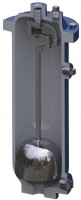
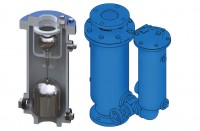

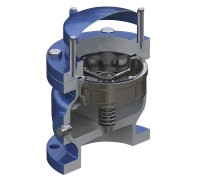

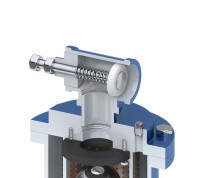